Technology Blog
FullShop System Helps One Company Increase Machine Hours by 30 Percent
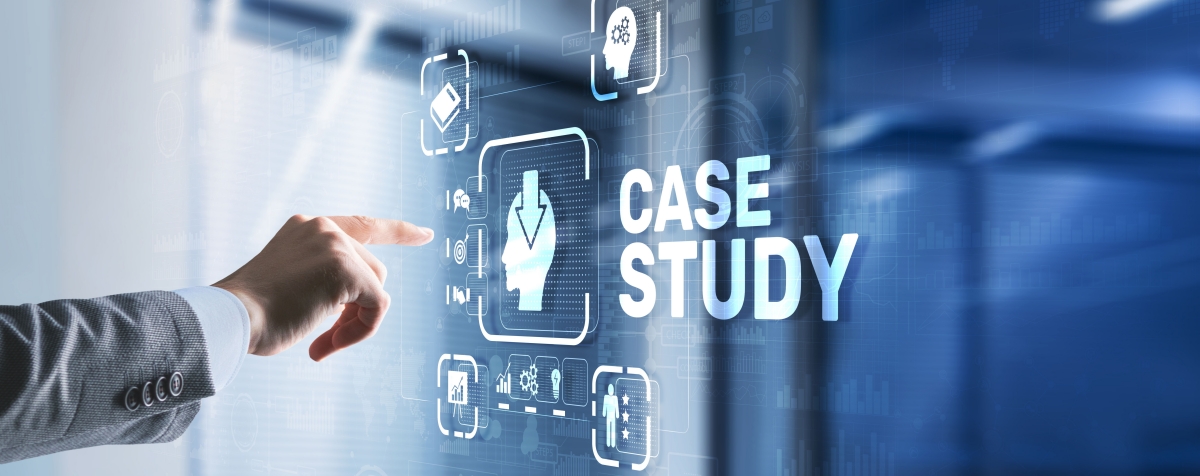
As we’ve started to deliver our FullShop™ Automated Coolant Delivery System, the results are in from one of our early users. By automatically supplying properly mixed coolant to machine tools, this system has recently helped one machining company maximize the value of its workforce, improve tool life and increase machine hours by over 30 percent.
A Leader in Advanced Manufacturing
Pequot Tool & Manufacturing specializes in precision machining and fabrication for a range of industries, including aerospace, electronics, industrial equipment and more. The Minnesota-based company has leveraged these capabilities to produce high-quality component parts and assemblies for over 30 years.
Recently, Pequot Tool wanted to diversify its capabilities to include unattended manufacturing processes. “One of the issues we had to overcome was our machines running out of coolant,” says Pequot Tool President Chad Shogren. “The coolant percentages were getting out of control, leading to poor tool life and potential catastrophic tooling failure.”
he Benefits of the FullShop™ System
To overcome these challenges, Pequot Tool installed our FullShop™ coolant system, eliminating the biggest barrier to unattended CNC machining: the need to replenish coolant in unattended machines.
After only six months with the FullShop™ system, Pequot Tool has seen many positive results:
- Coolant-related downtime has been eliminated
- Machinists no longer have to push coolant around the facility to maintain coolant levels—enabling them to focus on their craft
- Workers no longer have to divert time and energy to maintain proper coolant percentages for optimal tool performance
According to Shogren, the Pequot Tool staff loves the FullShop™ system, as it enables them to focus on producing the precision machined parts the company is known for. “It has also improved the predictability of tool life—allowing us to better maximize our labor for unattended operations. This was a big deal for us; prior to FullShop™, we thought 110 to 120 hours from a work center meant a good week. Now, it’s common for us to see 140 to 150 hours in unattended applications."
Shogren can also quantify his labor savings, using the time saved by FullShop™ to focus on secondary operations, maintenance or other value-added tasks. "We save on average 10 minutes of labor per machine daily—some more, some less," Shogren says. "With approximately 40 machines on the FullShop™ system, these savings total 400 minutes of labor a day that I can now use to create value. Because this is overhead, I can look at these 400 minutes as added profit to my bottom line. That's why FullShop™ was a no brainer for me!"
To learn more about how the FullShop™ system can benefit your machine tool operation, please visit: www.168mfg.com/system.