Technology Blog
Are You Focusing Too Much on Cutting Speed? Consider Your Coolant Choices Instead
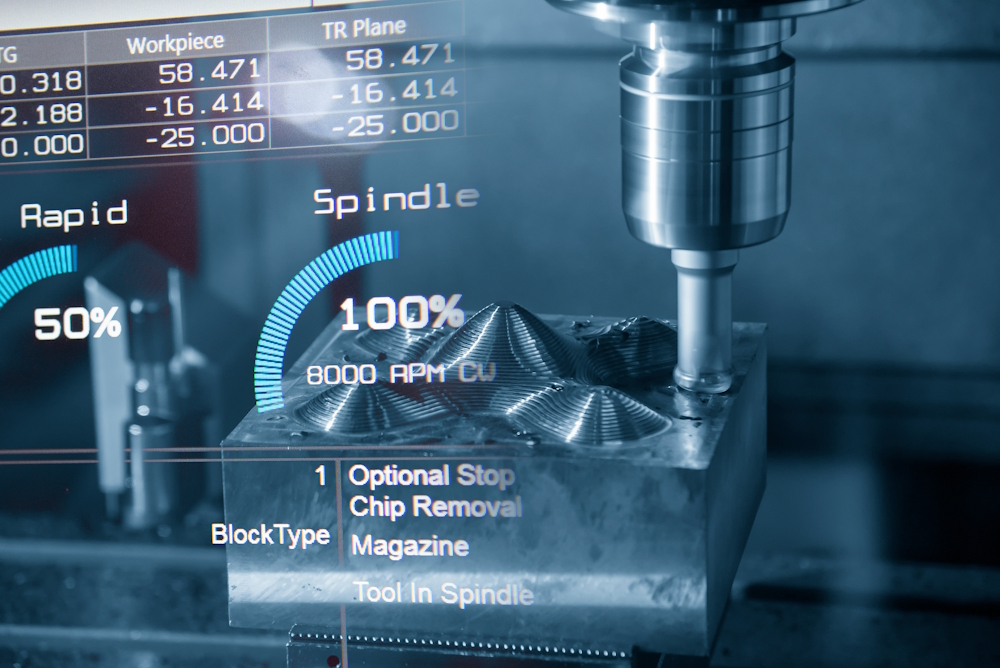
When it comes to optimizing machining parameters like unit cost and production rate, many shops still focus solely on spindle speed. But there’s more to the story.
A study, published in the International Journal of Engineering Research and Innovation, provides an in-depth technical analysis of how coolant impacts the machining process and uses the Taylor Tool Life Equation to quantify these effects. The Taylor Tool Life Equation is a fundamental principle in the study of tool wear and life expectancy in machining processes. It works by relating tool life to cutting conditions like speed, feed and depth of cut, along with the characteristics of the tool material and workpiece.
About the Experiments
Researchers introduced variables representing different types of coolants and lubricants into the Taylor Tool Life Equation to observe how the fluids influence the tool life constant (n) and cost per part (C). They also performed experiments, during which they used different coolant and lubricant types under controlled machining conditions, then measured the resulting tool wear, tool life and production costs. Using this data, they determined the impact of these fluids on the Taylor constants, C and n.
Key Research Findings
The researchers found significant variations in the Taylor Tool Life constants (C and n) based on the type of coolant. Their key observations included:
- Variability in tool life constants: The researchers found that concentration and application method significantly affected the Taylor Tool Life constant, n. This variability led to different tool life expectancies and machining efficiencies.
- Economic impact: They also found that changes in coolant led to variations in unit cost. For example, due to better tool life and less wear, the use of certain coolants resulted in a lower overall production cost despite higher individual tool costs.
- Stochastic variations: Finally, coolant properties have a stochastic nature, which could lead to unpredictable variations in tool life and production costs.
Putting It All Together
So what does this all mean for you and your machine shop? Understanding the impact of coolant on tool life and cost can lead to more informed decisions and optimal machining operations. Therefore, consider shifting your focus from traditional parameters like cutting speed to your coolant if you’re looking to improve tool life and operational efficiency.
At 168 Manufacturing, we can help you on your road to making better coolant choices. Our FullShop™ Automated Coolant Management System and Coolant Health App can help you improve the coolant delivery, monitoring and management processes — all while improving throughput, efficiency, ROI and tool life.
Contact us today to get started.
References